Understanding Tubing Fitting Sizes for Optimal Performance
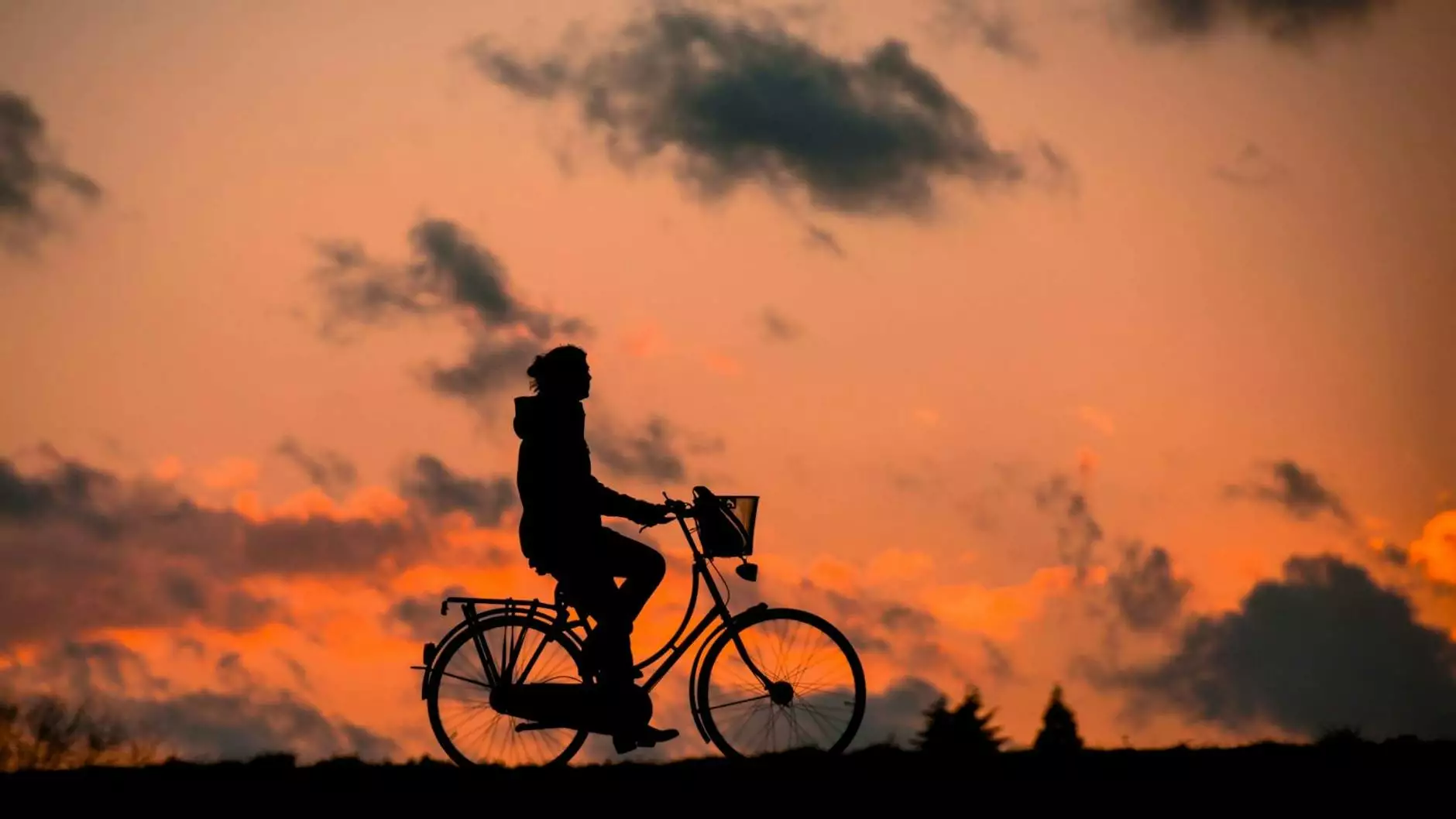
Tubing fitting sizes are an integral part of fluid applications across various industries, including oil and gas, automotive, and manufacturing. Knowing how to select the right tube fittings, along with their sizes and specifications, is essential for ensuring efficient and safe fluid systems.
The Importance of Choosing the Right Tubing Fitting Sizes
Selecting the appropriate tubing fitting sizes can have a significant impact on the performance and safety of your systems. Mismatched fittings can lead to leaks, reduced flow rates, and even catastrophic failures. The following factors emphasize the importance of making the right choice:
1. Safety
Using the correct tubing fitting sizes is crucial for preventing leaks, which can lead to hazardous conditions in many industrial environments. Proper fittings ensure that systems can withstand pressure without compromising safety.
2. Flow Efficiency
The diameter and configuration of tube fittings dictate fluid flow characteristics. Optimized fittings enhance flow efficiency, reducing energy costs and improving system performance.
3. Compatibility
Different metals, plastics, and rubber materials have various coefficients of expansion and compatibility with fluids. Ensuring size compatibility across your fittings helps maintain integrity and functionality.
Types of Tubing Fittings and Their Sizes
The market offers a wide range of tubing fittings tailored for specific applications. Here’s a detailed look at the different types of fittings available, their typical sizes, and their applications:
1. Tube Fittings
- Single Ferrule Tube Fittings: Typically used for lower pressure applications and are available in sizes ranging from 1/16” to 2”.
- Double Ferrule Tube Fittings: Ideal for high-pressure scenarios and available in sizes from 1/8” to 3”.
2. Ferrule Fittings
Ferrule fittings often come in specific sizing that aligns with standard tubing dimensions. They provide reliable seals and connect tubes securely. Common sizes range from 1/4” to 2”.
3. Forged Pipe Fittings
These fittings are available in robust materials, perfect for high-stress applications. Sizes generally range from 1/4” to 4”, depending on the design and application.
4. Threaded Pipe Fittings
Commonly used in plumbing and gas applications, threaded fittings come in multiple sizes. Common thread fittings are available in NPT configurations, with standard sizes from 1/8” to 2”.
5. Flanges
Flanges provide a flat surface for joining pipes and can accommodate various sizes, including but not limited to 1”, 2”, and larger custom dimensions depending on the requirement.
6. Valves
Valves like check valves, ball valves, and needle valves are also crucial components. Their sizes must match the piping system for optimal functionality. Sizes for valves typically range from 1/4” to 6”, thus covering a wide spectrum of applications.
Understanding Size Measurement Conventions
When dealing with tubing fitting sizes, it's crucial to understand the measurement conventions. The size designation usually refers to one of the following:
1. Outer Diameter (OD)
For tube fittings, the outer diameter is commonly used, especially when selecting components for hydraulic and pneumatic systems.
2. Inner Diameter (ID)
In some contexts, particularly with pipes, the inner diameter may be referenced since flow characteristics depend on the volume of fluid that can pass through.
3. Nominal Pipe Size (NPS)
The nominal size is often referred to as a convenience dimension that approximates the fitting's actual size. NPS can differ from the actual diameter and is essential for selecting compatible components.
Choosing the Right Tubing Fitting Sizes
Identifying the correct tubing fitting sizes requires a systematic approach:
- Identify the Application: Determine the application environment and pressure requirements. High-pressure systems require robust solutions.
- Check Compatibility: Ensure that the materials used for tubing and fittings are compatible with the transported fluids.
- Measure Accurately: Use calipers or gauges to measure the dimensions of existing tubing and fittings to ensure an exact match.
- Consult Manufacturer Guidelines: Refer to specifications and charts provided by manufacturers for accurate fitting size data.
Common Challenges with Tubing Fitting Sizes
Despite the availability of various options, choosing the right fittings can present challenges. Some common issues include:
1. Miscommunication of Size
Different regions sometimes use varied sizing conventions leading to confusion. Clarifying whether measurements pertain to OD or ID is critical.
2. Lack of Standardization
Although there are standard sizes, some manufacturers may have unique dimensions that make compatibility check-ups essential.
3. Changing Regulations
In some industries, regulations change, requiring adjustments in material and fitting choices. Staying informed about industry requirements can mitigate risks.
Conclusion
In conclusion, mastering the complexities of tubing fitting sizes is vital for professionals working in fluid handling systems. By understanding various types of fittings, sizing conventions, and common industry challenges, you can make informed decisions that enhance safety and performance in your operations. When in doubt, always consult with your manufacturer, like techtubes.in, to ensure that you're utilizing the best solutions for your specific applications. Properly selected and installed fittings can lead to years of trouble-free operations, ultimately elevating your business's efficiency and reliability.